Check out this (magnetic) conversation suspended magnets with Eriez Director of Minerals and Materials Processing Jose Martin. It will stick with you.
Edited by Donna Schmidt
Thanks for talking to North American Mining magazine exclusively about this topic, Jose. Can you explain, for those not in the know: What are the different types of suspended magnets? What are the uses, applications, or ideal placements for each?
Martin: There are two types of suspended magnets: suspended electromagnets and suspended permanent magnets. Suspended electromagnets are used for tramp metal collection from conveyed materials, improving life and performance of crushers downstream. They are also used to protect belts from objects that could easily cut the belting material of conveyors. They are usually mounted over conveyor belts and/or at the discharge of the conveyor to remove large pieces of tramp metal that could damage downstream crushers, mills, pulverizers, and grinders, as well as the actual belting of conveyors.
Electromagnets are mostly used in mining due to the size and strength of electromagnets as compared to permanent magnets. Suspended electromagnets are typically used on higher capacity conveyors, deeper burden depths, higher conveyor speeds and for added protection, especially for cone crushers in pebble crusher circuits.
Suspended permanent magnets are also used to remove unwanted iron from lighter burdens of material being conveyed on relatively slow-moving belts, which are typical of portable crushers and aggregates.
What are the biggest benefits and advantages of permanent suspended magnets?
Permanent suspended magnets do not face accidental shutdown due to power failure or fluctuation in strength. They operate at peak efficiency at all times without generating heat, and elevated temperatures have virtually no effect on these separators.
What are the most common misconceptions and myths associated with these magnets?
Permanent suspended magnets are stronger than electromagnets. While most of the applications for permanent suspended magnets are for low-capacity conveyors, electromagnets can be manufactured to accommodate very wide conveyors as wide as 3 meters or more. Even though there is an overlap on certain applications, electromagnets are the workhorses of the mining industry.
Unlimited weight support. While magnetic separators can hold significant weight tramp metal, there are practical limits based on magnet strength and system stability. Operators must perform frequent cleaning of manual clean magnets for effective protection.
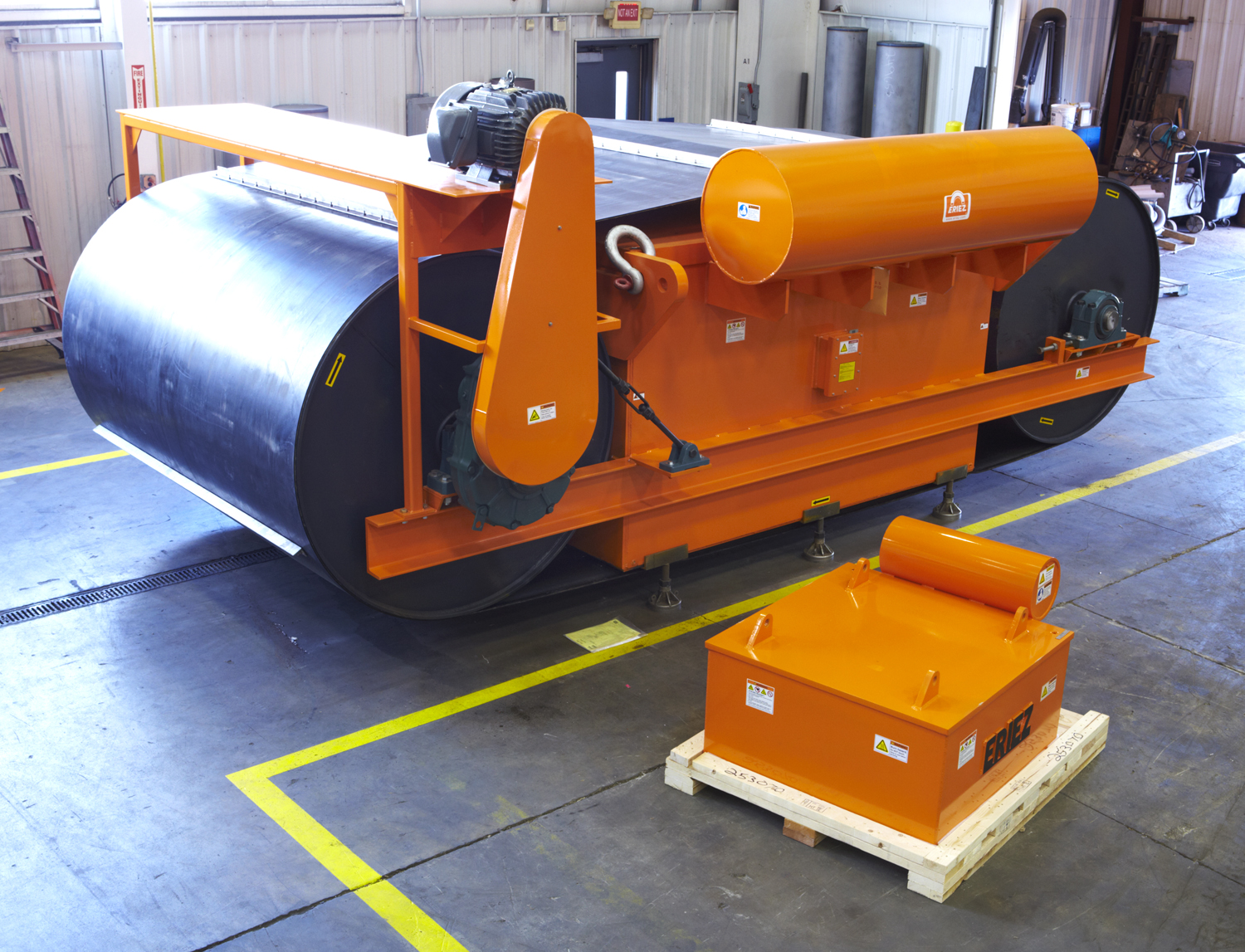
Can you talk about the maintenance of this equipment, and the safety factor?
Maintenance of suspended magnets depends on the type. Manual-cleaning units require no maintenance except for the removal of accumulated tramp iron. Self-cleaning models require regular belt tracking, bearing lubrication, V-belt tension check, and more. Eriez offers a 24/7 service hotline, OEM parts, on-site field service, equipment remanufacturing, and full “as new” warranties. For safety, Eriez advises that the magnets should be installed above conveyor belts away from working areas and that workers should not perform duties on this equipment unless it is shut down and the electric supply source is locked out.
How can this technology play a role in the critical minerals race?
In relation to critical minerals, Eriez offers a wide range of low- to high-intensity magnetic separators that are used in the concentration and purification of critical minerals. Some good examples where magnetic separators are used to concentrate ores include rare earth minerals, nickel and manganese. Other styles of high-intensity magnetic separators are also used to purify raw materials for lithium-ion batteries and those include lithium (carbonate, hydroxide and chloride) as well as graphite.
Eriez has a line of flotation equipment that is used in conjunction with magnetic separators to process hard rock spodumene mineral for the production of lithium.
Suspended magnets play a crucial role in:
- Metal Recovery and Separation: They remove tramp metal from conveyed materials in critical mineral extraction processes, enhancing product quality and protecting downstream equipment.
- Equipment Protection: They prevent damage to critical mineral processing equipment from tramp metal.
- Product Purity: They ensure the purity of critical mineral products by effectively removing metal contaminants.
- Resource Efficiency: They improve resource efficiency by removing unwanted metal contaminants during processing, allowing for the recovery and utilization of valuable minerals while minimizing waste.